Business Units
Engineering and Tool Manufacturing
Princeton Tool recognizes the need for shorter lead times to keep you ahead of the competition. We have found success in creating company standards that emphasizes quality and on-time deliveries by using cutting edge technology and advanced tool designs. We pride ourselves on being cost competitive and manufacturing a reliable quality tool with the goal of 100% compliance to your expectations.
Project management and job tracking tools are implemented to provide accurate data and a single point of contact, making sure your project receives the attention it deserves throughout its manufacturing process.
Our Tooling Departments continues to grow in capabilities, equipment, and staff. Currently, with over 25,000 ft³ of dedicated manufacturing space we can support multiple programs at one time to meet your delivery schedules.
Advanced Design and
Engineering Services
- Design of Complex Tooling Packages
- Specializing in Turbine Engine Blades/Vanes & Medical Components
- Prototype Tooling
- Part Geometry Modelling
- Gate Modelling
- Reverse Engineering
- CNC Programming
- Revision Control
Layout Services
Utilizing first article inspections, critical to quality points or a color plot we provide you an accurate statistical assessment of your new and legacy programs. The use of our 3d scanners and reports can provide you with the resolution and detail required to make critical decisions as they pertain to the quality of your product.
With our background in turbine engines and the components that make these engines, allows us to provide you the required information to save your team countless hours.
Wax Injection and Mold Assemblies
Princeton Tool has supported the investment casting industry for more than 23 years. The wax patterns and mold assembly business unit services major foundries across the United States of America providing alternatives to injecting and preparing waxes in house. This allows you to keep valuable floorspace previously supporting the many steps of producing wax molds, and re-allocating that space to increase throughput by enhancing dip lines, mold storage, and furnaces.
When Princeton Tool started its wax operation supporting nozzle assemblies. The service quickly expanded once customers experienced the level of support and quality they would receive when working with Princeton Tool. Through our three-shift coverage we are setup to support not only your low volume programs but also your high volume programs too.
In addition, to support injection and wax assemblies Princeton Tool provides periodic checks on product conformity through its blue light system. This process was started to verify pattern accuracy and to avoid the cost of non-conforming castings. Princeton Tool has seen this as a real benefit when customers want to qualify new waxes and or make wax die changes. This inspection method allows you to check pattern conformity to foundry specific tolerances as well comparisons to old revisions of the same part through our statistical analysis package.
Precision Machining
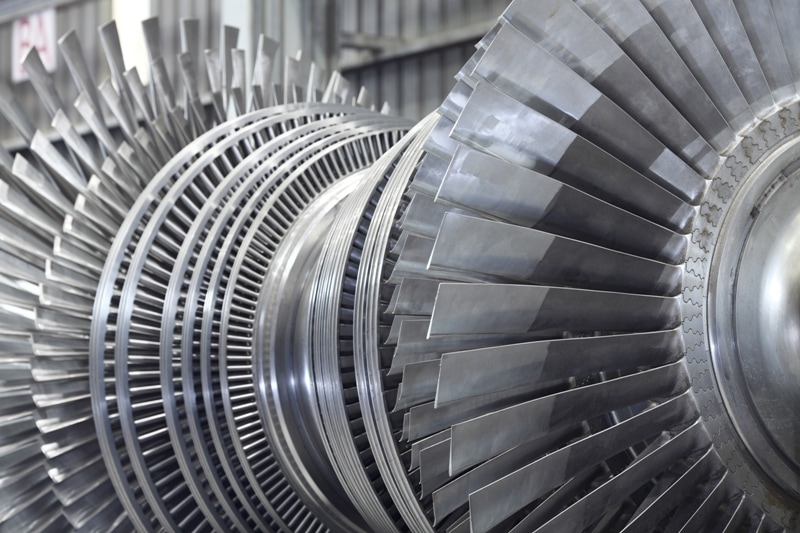
From coast to coast, Princeton Tool is known for its diverse and creative machining techniques. Areas of specialty include machining of investment castings produced across the country and around the world. Our foundry support service focuses on complex products manufactured for the aerospace and industrial gas turbine industries. When subsequent machining is needed, Princeton Tool’s seasoned sales and engineering team map out a machining plan for your product. Working closely with the product engineering staff, the process of mapping the machining plan helps eliminate program delays, ensuring the most efficient machining plan is generated saving both time and money. Rest assured, the capabilities of Princeton Tool provides the quickest and most effective path in getting your product to market.
The following capabilities are included with your cast product:
- Design and manufacture complex tooling, machining fixtures and gages.
- Fine tune gate design, targeting efficient removal later in process.
- Establish machining plan.
- Development of machining operation in a controlled environment.
- Support of high volumes of product throughput.
- Inspect and adjust machining operations using blue light technology to drive accuracy.
- Provide dimensional feedback (FAI).
- Generation of all quality documentation in accordance of AS9100 standards.
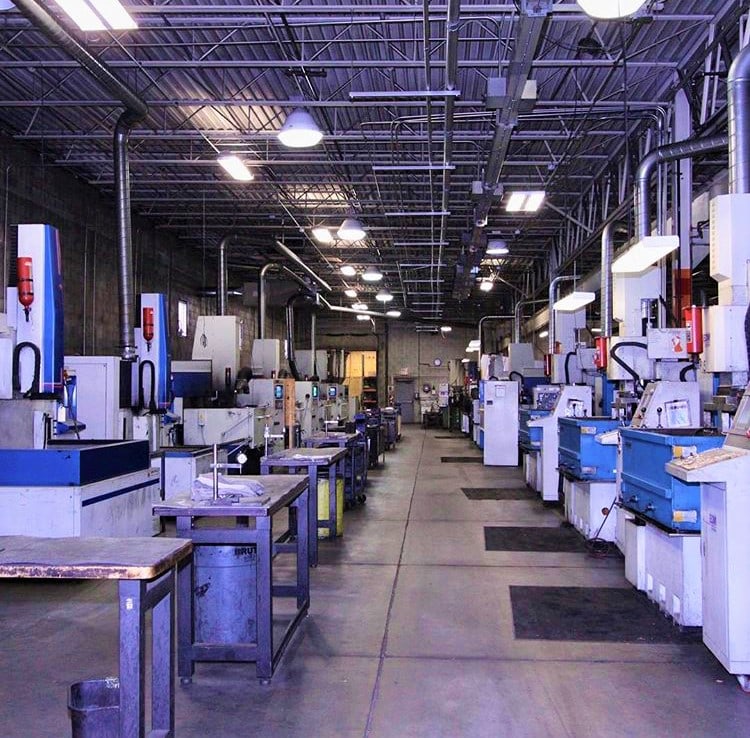
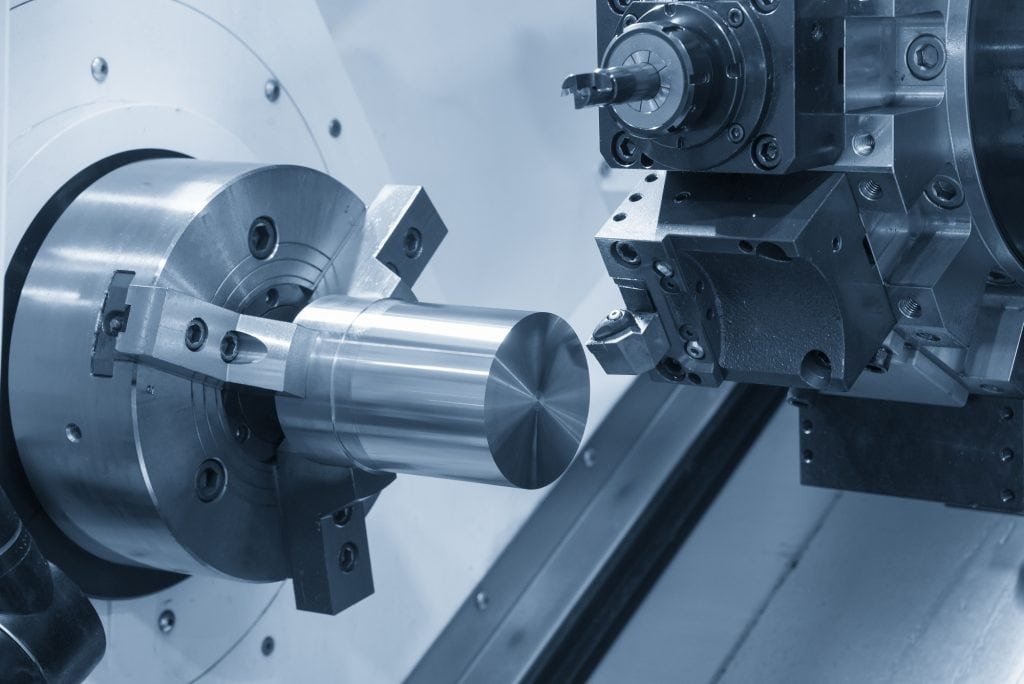
Princeton Tool is a manufacturing company that can be truly considered an all-encompassing operation. Once a program is placed with Princeton Tool, all services required to develop a process can be found internally or as part of Princeton Tool’s supply chain. Our supply chain relationships allows control of services outside of Princeton Tool’s offerings eg., non-destructive testing (FPI, X-Ray), Heat Treat, Welding, Coatings, and much more.
With over twenty years of post-cast processing, Princeton Tool understands the expectations of turning your product in a manner that supports your demands. You receive a service that meets your quality, budget, and schedule requirements at a fixed rate.
Turbomachinery
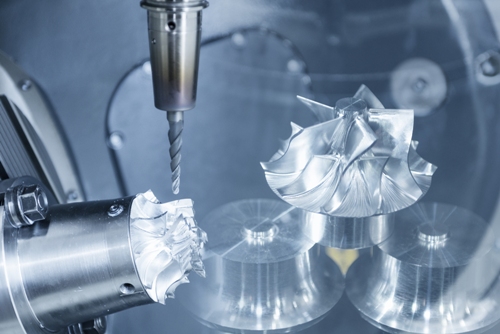
With the recent acquisition of Paragon Precision and the 75 years of experience, Princeton Tool’s expertise extends through hands-on, 5 axis programming combined with manufacturing engineering aligned toward production manufacturing while maintaining our rapid response prototyping capabilities as a job shop. Our programmers and engineers typically have 25 years of experience with complex products we so competently produce. For more information on Paragon Precision, please visit www.Paragon-Precision.com
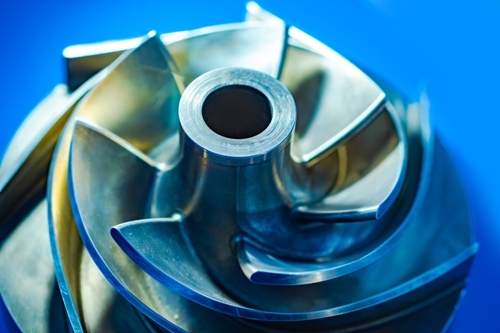
Our demonstrated, repeatable capability is the fabrication, and precision machining of high-performance, complex-shape, close-tolerance parts from high-strength, high-temperature, and corrosion-resistant exotic alloys as well as unscintered ceramic materials. These metallic alloys include Titanium, Inconel, Waspaloy, Hastolloy, Haynes 188, K-Monel, Rene-41, Udimet, A-286, CRES and mono-crystal alloys.
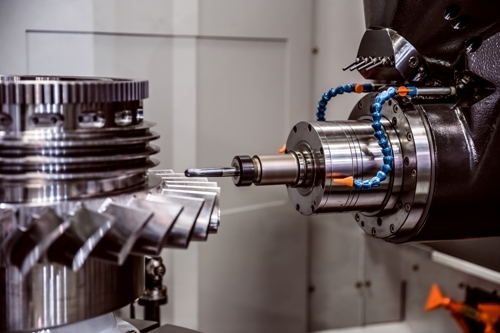
All activities are geared toward the on-time delivery of fully compliant items while providing the best value to our customer-partners. With the support of an ERP system and dedicated project manager, we provide a single point of contact to answer any questions necessary throughout the program.
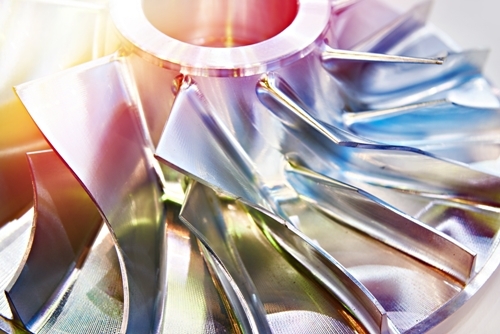
Through our knowledge base, experience, expertise, and equipment we are equipped for generating complex surfaces such as those encountered in turbomachinery components.